Composite Extruder Processes
Melt Pressure Sensor Applications for Composite Extruder Processes
Composite material is a new material formed without chemically dissolving and mixing of two or more materials. The purpose of composite production is to add new features to the materials that are not suitable on their own and that cannot be dissolved in each other, in order to give them suitable properties for their usage areas. (Strength, lightness, flexibility, cost, etc.)
Composite materials consist of at least one matrix and fiber material. If desired, other additives (fillers, UV stabilizers, etc.) can be added. The purpose of composite production is to add new features to the materials that are not suitable on their own and that cannot be dissolved in each other, in order to give them suitable properties for their usage areas. (Strength, lightness, flexibility, cost, etc.)

Composite materials form their main structure from two components;
* Matrix Material (Polymer, metal and metal alloy, ceramic-based materials.)
* Reinforcement Material (Steel, carbide, aramid, nylon etc.)
Composites generally get their strength from hard and brittle reinforcement materials. Matrix materials give the composite toughness and ductility. The task of holding the materials together is also in the matrix material. Due to the high strength and lightness of the composite material, its usage area is wide.
General Parts;
Extruder, Hopper, Die.
Working Principle;
Injection Technique (Closed Molding)
It is a preferred method in the manufacture of fiber-reinforced thermoplastics. It is possible to use injection machines capable of molding parts ranging from a few grams to ten kilograms in each molding period. The molding compounds fed to the injection machines are premixes in the form of granules ranging in length from 3-6 m. Injection molding generally uses pallet-shaped premixes.
What is a Melt Pressure Sensor?
Melt Pressure Sensor is an instrument used to measure the pressure and temperature of melted liquids (optional) in processes where plastic raw materials can reach high temperatures.
Why is a Melt Pressure Sensor Necessary?
Almost all extruders use at least one melt pressure transducer because it is desirable for melt pressure/temperature control to improve the quality of the extrusion process.
* Safety,
* Equipment Protection,
* Higher Efficiency,
* Higher Product Quality.
Melt Pressure Sensor Applications for Composite Manufacturing Extruder Processes;
* Melt Pressure Sensor in Mold / Melt Pressure Control Application
* Pre-Filter Melt Pressure Sensor / Melt Pressure Control Application
* Post Filter Melt Pressure Sensor / Melt Pressure Control Application
* Melt Pressure / Melt Pressure Control Sensor Application Before Melt Gear Pump
* Melt Pressure Sensor After Melt-Gear Pump / Melt Pressure Control Application
* Chips Cutters Melt Pressure Sensor / Melt Pressure Control Application
Aim:
* Melting pressure, controlling flow stability,
* To ensure the formation of the necessary pressure for production,
* To monitor possible contamination that may clog the filter changer and cause pressure drop in the mold, and as a result, to determine that clogged filters should be replaced, (Therefore, the pressure is measured before and after the screen changer.)
* The gear pump is used to give a constant flow rate to the mold: the flow is adjusted based on the measured pressure value (The pressure value is used to give feedback to the driver for screw speed adjustment.)
* Creating the necessary recipes for production,
* Evaluation of plastic raw materials,
* Controlling Pressure,
* Preventing the formation of excessive pressure on the screw,
* Protecting screw wear.
Please contact us for more detailed technical information about your Machine and Equipment needs related to Melt Pressure Sensors and Extrusion Lines that you may need in Composite Extruder Processes.

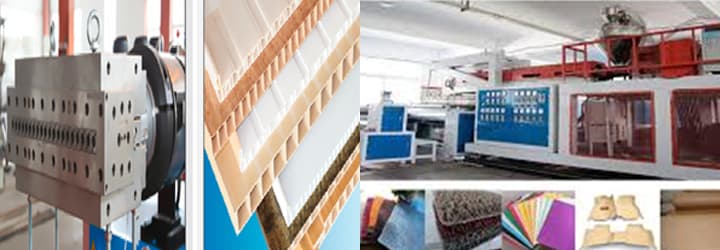
