Yarn Production Extruder Processes
The yarn production machine consists of feeding and dosing, extrusion, filtration, metering and pumping, spinning with nozzles, cooling, lubrication, stretching, blowing, centering and winding stages. While polypropylene yarn is produced by going through these stages, a raw material dryer is also required for polyamide yarn production, and a crystallizer and dryer are required for polyester yarn production.
The machine, all units of which are controlled with the help of a central computer, operates fully automatically. Electric motors are driven by vector-controlled AC frequency inverters in the machine, where the need for compressed air is met by a screw compressor and a chiller group equipped with an automatic controlled air conditioning system is used in the cooling system.
Pressure sensors, thermocouples and necessary interface cards are used in the automation of the system. Single inlet and four outlet planetary gear system polymer metering pumps are preferred to measure the required polymer at the desired rate and transfer it to the nozzles. In the cooling cabinet, where the polymer solidifies and takes the form of yarn, air cooling is provided and the air temperature is controlled by a computer in the unit designed to obtain a laminar and desired smooth air flow.
For the production of BCF yarn, the machine has a pressurized, hot air jet texturing unit and air jet centering system. The machine is equipped with winding units with automatic bobbin changer.
General Parts:
Extruder, metering pumps, die assembly, web forming and winding system.
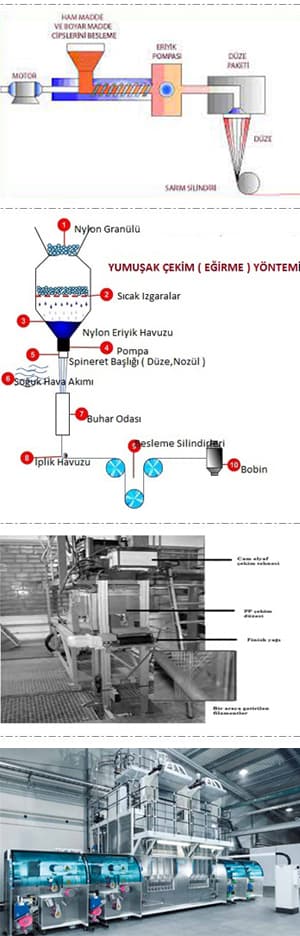
Working Principle:
A wide variety of methods have been developed for producing shaped objects from granules or powdered plastics.
What is a Melt Pressure Sensor?
Melt Pressure Sensor is an instrument used to measure the pressure and temperature of melted liquids (optional) in processes where plastic raw materials can reach high temperatures.
Why is a Melt Pressure Sensor Necessary?
Almost all extruders use at least one melt pressure transducer because it is desirable for melt pressure/temperature control to improve the quality of the extrusion process.
Safety
Equipment Protection
Higher Efficiency
Higher Product Quality
Melt Pressure Sensor Applications for Yarn Production Extruder Processes;
Pre-Filter Melt Pressure Sensor / Melt Pressure Control Application
Post Filter Melt Pressure Sensor / Melt Pressure Control Application
Melt-Gear Pump Pre-Melt Pressure / Melt Pressure Control Sensor Application
Melt-Gear Pump Post Melt Pressure Sensor / Melt Pressure Control Application
Aim:
*Checking the melt pressure, flow stability,
* To ensure the formation of the necessary pressure for production,
*Monitoring for possible contamination that could clog the filter changer and cause pressure drop in the mold, and as a result to determine if clogged filters need to be replaced (therefore the pressure is measured before and after the screen changer)
*The gear pump is used to give a constant flow rate to the mold: the flow is adjusted based on the measured pressure value (the pressure value is used to give feedback to the driver for screw speed adjustment)
*Creating necessary prescriptions for production,
* Evaluation of plastic raw materials,
*Controlling Pressure,
*Preventing excessive pressure on the screw,
* Protecting screw wear,


