Textile Production Extruder Processes
In defining the term microfiber, the fiber diameter or filament number in dtex or denier is generally taken into account. Accordingly, fibers in the range of 0.1-1.0 dtex are defined as microfibers [1, 2]. Fibers thinner than 0.1 dtex are called super microfibers. Microfiber is 40 times finer than wool, 30 times finer than cotton, 10 times finer than silk, Continuous filament production, Direct fiber spinning method (conventional method) Any man-made fiber in the range of 0.1-1.0 dtex is defined as microfiber. The most produced man-made microfibers consist of polyester, nylon, polypropylene, acrylic and viscose. Microfibers are produced in the form of continuous filaments or staple staples, depending on the purpose of use. Compared to conventional fibers, microfibers provide fabrics with a luxurious appearance, improved physical and handling properties, and a high level of wearing comfort.
Therefore, there has been an increasing trend towards microfibers in recent years. Microfibers are widely used in many areas such as high quality clothes, evening dresses, sportswear, home textiles, industrial products. In defining the term microfiber, the fiber diameter or filament number in dtex or denier is generally taken into account. Accordingly, fibers in the range of 0.1-1.0 dtex are defined as microfibers. Fibers thinner than 0.1 dtex are called super microfibers. Microfiber is 40 times finer than wool, 30 times finer than cotton, and 10 times finer than silk.
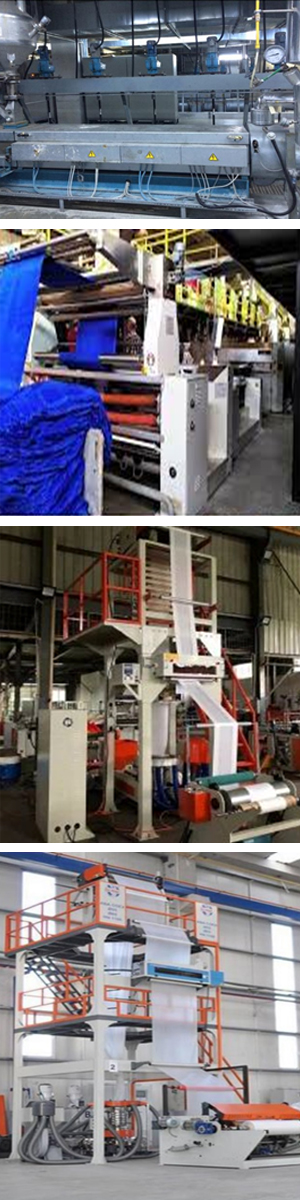
Microfiber production is divided into two as continuous filament and staple fiber. Continuous filament production method is carried out in two ways: direct fiber spinning (conventional fiber spinning) and bicomponent spinning method. As is known in conventional fiber spinning, the polymer is pressed into either gas (often air) or solution and then drawn. Before the polymers are passed through the nozzles, they are either melted or turned into solutions. Sending the polymers to the nozzles by melting is defined as pulling fiber from the melt, and using the polymer solution is defined as pulling fiber from the solution.
For this reason, the drawing method is generally used in the production of microfibers. Optimizing polymer viscosity (high shrinkage temperature reduces viscosity). Optimizing the nozzle design (arranging the nozzle holes to give homogeneous cooling). Optimizing the ambient temperature under the nozzle (controlling the cooling rate). Proper splicing of filaments (assembly closest to level). Optimizing the fiber draw (controlling the spinning tension). Low speed shooting (smooth polymer delivery).
General Parts
Extruder, metering pumps, die assembly, web forming and winding system.
Working Principle
A wide variety of methods have been developed for producing shaped objects from granules or powdered plastics.
What is a Melt Pressure Sensor?
Melt Pressure Sensor is an instrument used to measure the pressure and temperature of melted liquids (optional) in processes where plastic raw materials can reach high temperatures.
Why is a Melt Pressure Sensor Necessary?
Almost all extruders use at least one melt pressure transducer because it is desirable for melt pressure/temperature control to improve the quality of the extrusion process.
Safety
Equipment Protection
Higher Efficiency
Higher Product Quality
Melt Pressure Sensor Applications for Textile Manufacturing Extruder Processes;
Melt Pressure Sensor in Mold / Melt Pressure Control Application
Pre-Filter Melt Pressure Sensor / Melt Pressure Control Application
Post Filter Melt Pressure Sensor / Melt Pressure Control Application
Melt-Gear Pump Pre-Melt Pressure / Melt Pressure Control Sensor Application
Melt-Gear Pump Post Melt Pressure Sensor / Melt Pressure Control Application
Chip Cutters Melt Pressure Sensor / Melt Pressure Control Application
Aim:
*Checking the melt pressure, flow stability,
* To ensure the formation of the necessary pressure for production,
*Monitoring for possible contamination that could clog the filter changer and cause pressure drop in the mold, and as a result to determine if clogged filters need to be replaced (therefore the pressure is measured before and after the screen changer)
*The gear pump is used to give a constant flow rate to the mold: the flow is adjusted based on the measured pressure value (the pressure value is used to give feedback to the driver for screw speed adjustment)
*Creating necessary prescriptions for production,
* Evaluation of plastic raw materials,
*Controlling Pressure,
*Preventing excessive pressure on the screw,
* Protecting screw wear,

