Blow Molding Extruder Processes
Plastic injection method is one of the economical and popular methods of producing a wide range of plastic consumables. With this method, products such as vehicle panels, computer parts, household goods can be produced. These products can be produced in different sizes using the plastic injection method and through mass production to meet various needs.
With this method, manufacturing can be done using thermoplastics, thermosets and some elastomers. The method is based on the principle that the plastic raw material is melted with the help of heat and then pressed into a mold and brought into the desired shape. While the raw material comes to the desired shape, it cools in the mold and the part is removed from the mold. With the technological developments, parts from 15 grams to about 23 kilograms can be manufactured with this method.
Extrusion Blow Molding Machine Process
1. Extrusion Blow (Continuous, Accumulative and Co-Extrusion)
2. Stretch Blow
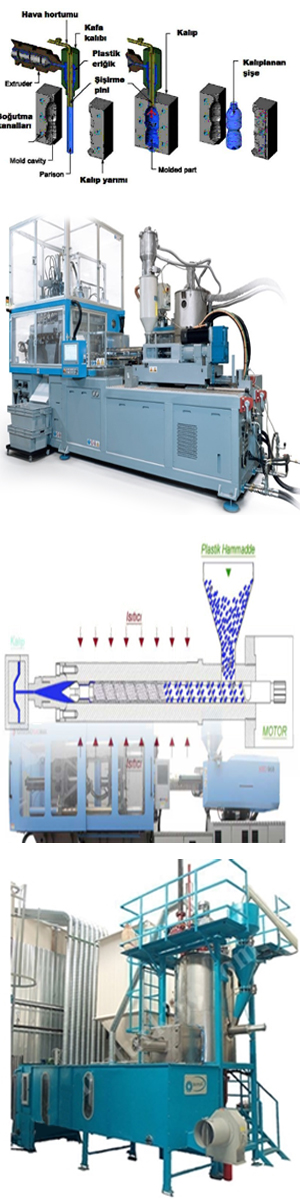
3. Injection Inflator
4. Injection Stretch Blow
Apart from this, there are also submersion method (bottom blow molding) and rotation method (molding with rotation) in the world blow molding technologies. Extrusion blow molding technology, where we can find the applications mentioned above, is one of the most used methods in the blow molding world.
General Inflation Methods and Order of Operation; The Blow Molding Process is divided into two different subgroups in terms of blowing logic, extrusion blowing and stretch blowing. To explain briefly; In the stretch blow molding process, the preforms molded with an injection machine are reheated and stretched with the help of an inflation rod, and these stretched preforms are blown and remolded with compressed air.
Apart from the steps listed above, it is possible to increase the steps of the process by connecting optional equipment to the machine in order to label the product or perform leak testing. For containers of very large volumes, welding devices are also included in the process to securely join the exposed end of the parison. If we examine an extrusion blow molding machine, we see that it is divided into several subsystems as described below;
General Parts:
Injection Unit, Molding Unit, Vise Unit.
Working Principle:
In the raw material drying unit, it is kept at the appropriate temperature for a sufficient time according to the characteristics of the raw material to be used in the process.
Plasticizing Stage:
The cover of the dried raw material feeder is opened and pushed towards the heating units with the help of the worm screw. Here, the melted material, passing through heaters at different temperatures, moves towards the injection nozzle. The temperatures of the heaters are determined by considering factors such as the melting temperature of the raw material to be used, the fluidity value, the part wall pediment. General Inflation Methods and Order of Operation; The blow molding process is divided into two different subgroups in terms of blowing logic, extrusion blowing and stretch blowing. To explain briefly; In the stretch blow molding process, the preforms molded with an injection machine are reheated and stretched with the help of an inflation rod, and these stretched preforms are blown and remolded with compressed air.
The Basic Steps of the Extrusion Blow Molding Process are as Listed Below;
1. Plasticizing and preparing the thermoplastic raw material in an extruder,
2. Directing the molten plastic with a vertical flow,
3. Turning the molten raw material into a fluid hose called parison and pouring it out of the head,
4. The parison flow head is also called simply head, extrusion head, inflation head and parison head,
5. Clamping the parison flowing from the head between a mold with the help of a vise,
6. Inflation pins or inflation needles (or valves) getting into the closed mold,
7. Inflating the parison between the mold walls cooled with cooling water with compressed air by means of inflation pins and
removal of throat burrs at the end of the inflation process,
8. The mold is opened and the inflated product hangs on the inflation pin,
9. Deburring of the blown product in the edge areas.
What is a Melt Pressure Sensor?
Melt Pressure Sensor is an instrument used to measure the pressure and temperature of melted liquids (optional) in processes where plastic raw materials can reach high temperatures.
Why is a Melt Pressure Sensor Necessary?
Almost all extruders use at least one melt pressure transducer because it is desirable for melt pressure/temperature control to improve the quality of the extrusion process.
Safety
Equipment Protection
Higher Efficiency
Higher Product Quality
Melt Pressure Sensor Applications for Blow Extruder Processes;
Melt Pressure Sensor in Mold / Melt Pressure Control Application
Aim:
*Checking the melt pressure, flow stability,
* To ensure the formation of the necessary pressure for production,
*Creating necessary prescriptions for production,
* Evaluation of plastic raw materials,
*Controlling Pressure,
*Preventing excessive pressure on the screw,
* Protecting screw wear,
