Rubber Extruder Processes
Rubber performance extruders, rubber and various series of materials such as EPDM, NBR and Neoprene; It is used to provide high capacity and high mixing performance in extrusion applications such as hose, profile, bellows and roving.
General Parts:
It consists of raw material feeding hopper, extruder driven motor, gear reducer box, screw and barrel, heaters, cooling fan form molds, hopper and control cabinet.
Working Principle:
The raw material is melted from the chamber and taken out of the mold in the desired form at the end with the pressure support in the extruder and drawn in the desired dimensions. The product is drawn under constant temperature to ensure the continuity of the form in a stable state.
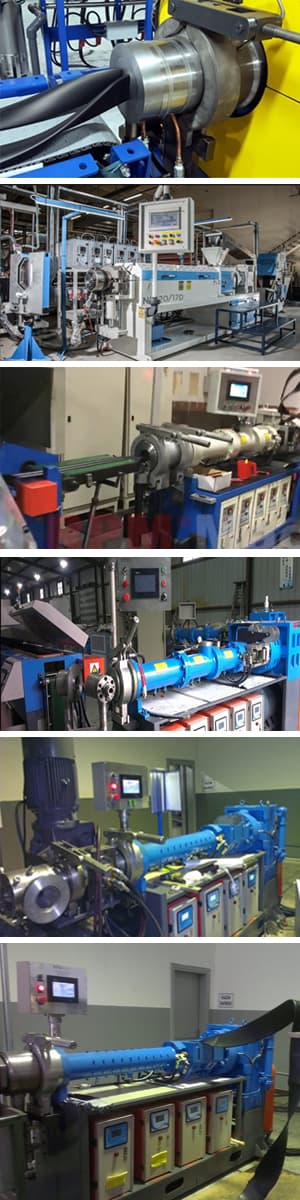
What is a Melt Pressure Sensor?
Melt Pressure Sensor is an instrument used to measure the pressure and temperature of melted liquids (optional) in processes where plastic raw materials can reach high temperatures.
Why is a Melt Pressure Sensor Necessary?
Almost all extruders use at least one melt pressure transducer because it is desirable for melt pressure/temperature control to improve the quality of the extrusion process.
Safety
Equipment Protection
Higher Efficiency
Higher Product Quality
Melt Pressure Sensor Applications for Rubber Extruder Processes;
Melt Pressure Sensor in Mold / Melt Pressure Control Application
Aim:
* Checking the melt pressure, flow stability,
* To ensure the formation of the necessary pressure for production,
* Creating necessary prescriptions for production,
* Evaluation of plastic raw materials,
* Controlling Pressure,
* Preventing excessive pressure on the screw,
* Protecting screw wear,