Granular Extruder Processes
The ISO Standard Series Plastic Single Screw Extruder Machine is the core part of the core processes in polymer processing and is also a key component in many other processes. The most important purpose of a single screw extrusion process is to create pressure in a polymer melt so that it can be extruded through a die or injected into a die. Most of the machines are plasticizing: they bring in solids or in powder form and melt them as well as building pressure.
General Parts:
The single screw extruder is composed of driven motor, gear reducer box, screw and barrel, die-cast aluminum heater, cooling fan, hopper and control cabinet.
Working Principle:
The working principle of the single screw extruder is as follows: When the screw rotates, it moves the resin inside the hot barrel. In this way, it reaches the required temperatures and mixtures to form a homogeneous melt. The pressure created by single screw extruders then forces the melt through the extruder. It comes out in the form of a mold. The whole system has a barrier screw that ensures that all the resin does not melt at the base extrusion screw. The “resin” in powder or granular form is put into the feeding hopper, the powder or granule comes to the heating roller, it softens and melts as a result of the heat or friction it receives while being pushed forward by the “extrusion screw”. A certain amount is stored at the cylinder end. It is forced to pass through the "mould", the product that comes out of the mold has taken the shape of the "mould interior". It is passed through a regular “cooling system”, “Measure control” and “Length adjustment” are made. The product is removed by "cutting" to the desired length, "Conveyor" or another system.

What is a Melt Pressure Sensor?
Melt Pressure Sensor is an instrument used to measure the pressure and temperature of melted liquids (optional) in processes where plastic raw materials can reach high temperatures.
Why is a Melt Pressure Sensor Necessary?
Almost all extruders use at least one melt pressure transducer because it is desirable for melt pressure/temperature control to improve the quality of the extrusion process.
Safety
Equipment Protection
Higher Efficiency
Higher Product Quality
Melt Pressure Sensor Applications for Granular Extruder Processes;
Pre-Filter Melt Pressure Sensor / Melt Pressure Control Application
Post Filter Melt Pressure Sensor / Melt Pressure Control Application
Melt-Gear Pump Pre-Melt Pressure / Melt Pressure Control Sensor Application
Melt-Gear Pump Post Melt Pressure Sensor / Melt Pressure Control Application
Aim:
*Checking the melt pressure, flow stability,
* To ensure the formation of the necessary pressure for production,
*Monitoring for possible contamination that could clog the filter changer and cause pressure drop in the mold, and as a result to determine if clogged filters need to be replaced (therefore the pressure is measured before and after the screen changer)
*The gear pump is used to give a constant flow rate to the mold: the flow is adjusted based on the measured pressure value (the pressure value is used to give feedback to the driver for screw speed adjustment)
*Creating necessary prescriptions for production,
* Evaluation of plastic raw materials,
*Controlling Pressure,
*Preventing excessive pressure on the screw,
* Protecting screw wear,


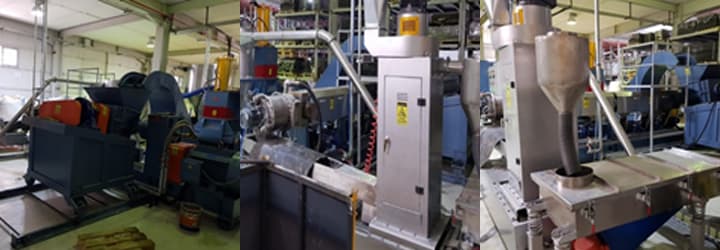
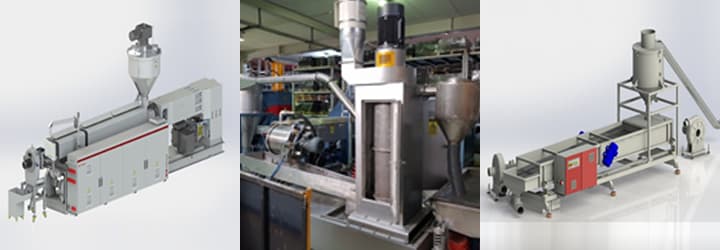